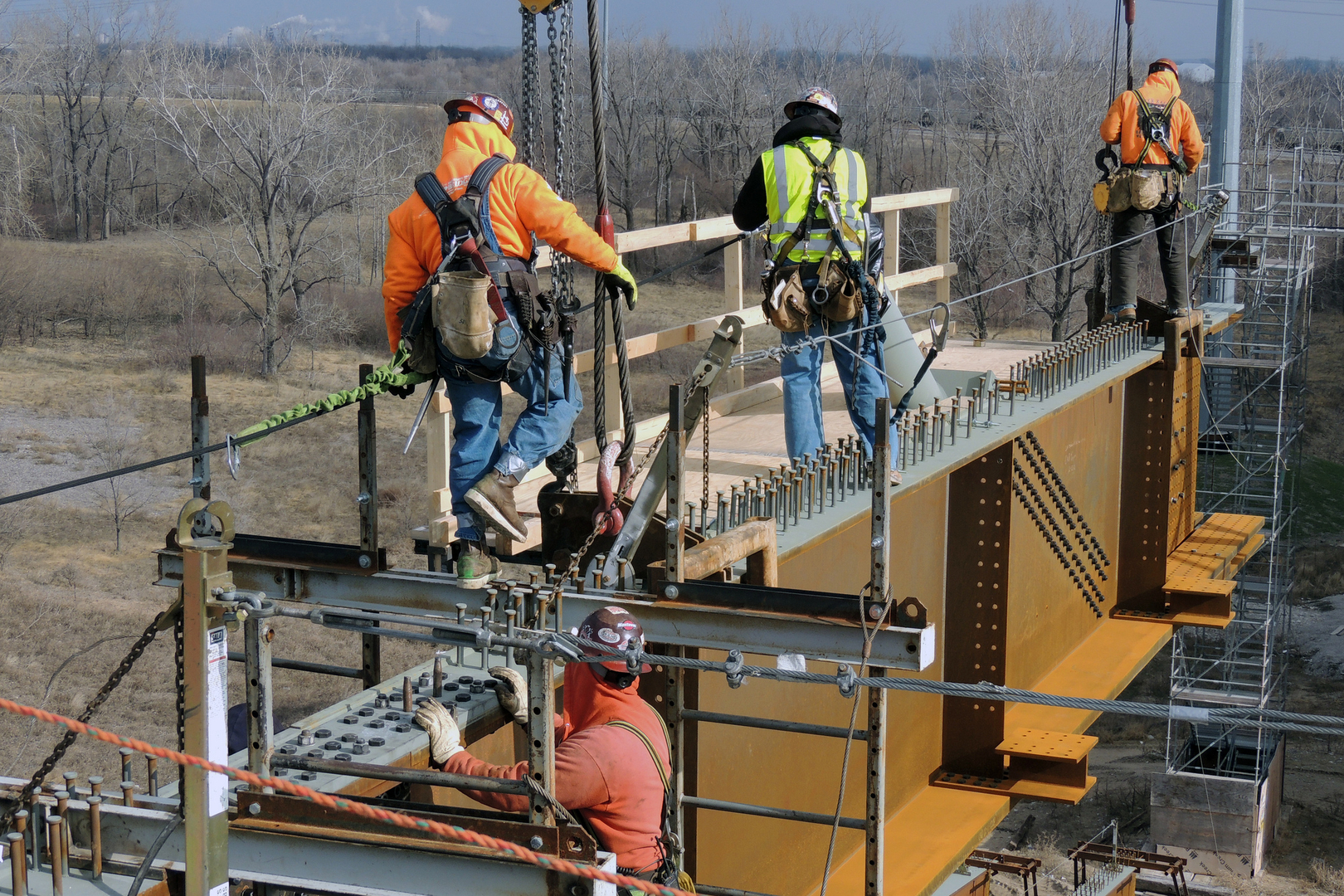
Conveyor systems are the backbone of many industries, providing a reliable and efficient means of transporting goods and materials. Industries such as manufacturing, logistics, mining, and food processing rely heavily on conveyors to keep operations running smoothly. However, ensuring the continuous performance of these systems requires the expertise of conveyor technicians who are responsible for their installation, maintenance, and troubleshooting. These technicians face several common difficulties, ranging from mechanical breakdowns to safety concerns.
Conveyor systems are subject to constant motion, and over time, components such as belts, rollers, bearings, pulleys, and motors experience wear and tear. These components often wear down under the strain of continuous operation, resulting in inefficiencies, breakdowns, and costly repairs. For example, worn-out bearings can cause friction, leading to motor failure, while stretched or frayed belts can result in slippage or system stoppage.
To mitigate this issue, it’s essential to implement a robust preventive maintenance program. Regular inspections and monitoring are critical in identifying parts that show signs of wear. Technicians should focus on high-risk areas such as bearings and rollers, checking for unusual sounds or vibrations, as these can signal potential failure. Vibration analysis tools, infrared thermography, and ultrasonic testing are valuable techniques that can help detect signs of wear early before they result in significant damage. Additionally, conveyor technicians should suggest using high-quality, durable materials that are more resistant to wear, reducing the frequency of component replacements.
Misalignment of the conveyor belt is a common issue that can lead to a range of operational problems, including uneven wear, reduced efficiency, and even complete system failure. Misalignment can occur due to several factors, including improper installation, material build-up, or inadequate tensioning. When the belt becomes misaligned, it places additional strain on the system, causing it to slip, leading to costly downtime and potential damage to the equipment.
Ensuring proper belt alignment is critical for the efficient functioning of the conveyor system. Technicians should regularly check the alignment of the belt during routine maintenance and correct any misalignment immediately. Using laser alignment tools can greatly improve the accuracy of belt adjustments, ensuring that it runs in the correct position. Additionally, checking the tension of the belt regularly and making adjustments as necessary can help avoid slippage. Technicians should also inspect the pulleys and rollers to ensure they are free from material build-up, as this can also lead to misalignment.
Overloading is a serious issue that can compromise the integrity of a conveyor system. Many times, technicians are called to address problems caused by the conveyor being subjected to loads that exceed its design capacity. Overloading can strain the belts, motors, pulleys, and rollers, causing premature failure of key components. In addition, overloading can reduce the system's overall efficiency, resulting in slower production rates and higher operational costs.
To prevent overloading, it’s important for technicians to ensure that the conveyor is designed to handle the specific load requirements of the operation. The system should be regularly inspected to ensure it is operating within its recommended capacity. For operations where the load regularly fluctuates or increases, technicians can recommend upgrading the system to accommodate higher loads or adding supplementary conveyor units to help distribute the load more evenly. Moreover, implementing load sensors and automatic shut-off mechanisms can help prevent the system from being overloaded, ensuring that the conveyor shuts down if the load exceeds the limit.
Conveyor systems rely heavily on electrical and control systems to function. These systems are responsible for regulating the speed, direction, and overall performance of the conveyor, making them crucial for efficient operation. However, like any electrical system, they are prone to faults, including circuit issues, sensor malfunctions, or wiring failures. Electrical failures can cause the system to stop unexpectedly, leading to downtime and delays in production.
For technicians to address electrical issues effectively, a solid understanding of the system’s electrical schematics is required. Routine testing of control systems is essential to detect any faults before they become major problems. Technicians should be proficient in using diagnostic tools such as multimeters, oscilloscopes, and circuit testers to check the condition of the wiring and control components. Regular calibration and inspection of sensors are equally important, as even slight inaccuracies can affect the overall performance of the system. Furthermore, ensuring that all electrical connections are secure and properly insulated will reduce the risk of electrical failures.
Many conveyor systems are used to transport a wide variety of materials, including those that may be sticky, greasy, dusty, or corrosive. Over time, foreign materials can accumulate on the conveyor components, causing a range of issues. For instance, dust and debris can clog up bearings and rollers, while sticky substances can cause the conveyor belt to slip or become clogged. When foreign materials interfere with the functioning of the conveyor system, it can lead to poor performance, excessive wear, and even breakdowns.
To address the problem of foreign material interference, technicians need to implement regular cleaning schedules for the conveyor system. Regular cleaning helps remove dust, dirt, and other debris that may have accumulated on the system’s components. Depending on the materials being transported, it may be necessary to use specialized cleaning solutions or equipment. For sticky materials, the conveyor belt itself may need to be replaced with a non-stick surface or a specialized belt designed for handling such materials. Technicians should also ensure that the conveyor system is properly enclosed or protected, particularly in environments where contamination is more likely.
The complexity of modern conveyor systems requires technicians to possess a high level of technical expertise. However, the rapid pace of technological advancement can sometimes leave technicians with outdated skills, making it difficult for them to troubleshoot and repair newer conveyor systems. Insufficient training or lack of experience can lead to misdiagnosis, improper repairs, and ultimately costly downtime.
Technicians should be encouraged to continually update their skills through training programs, certifications, and hands-on experience. Employers should invest in training to ensure that technicians are equipped with the latest knowledge of new technologies, maintenance procedures, and safety protocols. A well-rounded approach to training, which combines theoretical learning with practical, on-the-job experience, ensures that technicians are capable of handling the variety of conveyor systems they may encounter. Mentorship programs, where more experienced technicians share their expertise, can also help less experienced technicians build their skills more quickly.
Conveyor systems can present a range of safety hazards, particularly when they are not properly maintained or when technicians are working on them without proper precautions. Common safety risks include entanglement in moving parts, contact with electrical components, and exposure to falling materials. Conveyor technicians are frequently exposed to these hazards during inspections, maintenance, and repair work, making safety a top priority.
To minimize safety risks, technicians should always follow established safety protocols, including lockout/tagout procedures, to ensure that the conveyor system is de-energized before any maintenance begins. Wearing appropriate personal protective equipment (PPE) such as gloves, helmets, and safety boots is essential for minimizing injury risk. Technicians should also be familiar with the location of emergency stop buttons and other safety features of the system. Safety training should be an ongoing process, with regular updates on new safety procedures, risk assessment techniques, and safe operating practices. Additionally, installing safety guards, emergency stop mechanisms, and safety sensors on the conveyor system can help protect technicians and operators from accidents.
Perhaps one of the most pressing concerns for conveyor technicians is the impact of downtime. Even a few hours of system failure can cause significant delays in production, leading to a loss of revenue and productivity. Diagnosing and addressing the issue quickly is essential to minimize downtime. Technicians are often under pressure to resolve problems as quickly as possible, but this can sometimes lead to rushed repairs that may not fully address the root cause of the issue.
To minimize downtime, technicians should prioritize routine maintenance to prevent breakdowns before they occur. By identifying and addressing potential issues during scheduled inspections, technicians can avoid unexpected failures. Additionally, keeping a stock of critical spare parts allows technicians to replace damaged components without waiting for external suppliers. Effective communication between maintenance teams, operators, and managers is also crucial to ensure that everyone is aware of the status of the conveyor system and the expected repair timeline.
The role of a conveyor technician is a challenging yet essential one in industries that rely on these systems for smooth operations. From wear and tear on components to electrical failures, foreign material interference, and safety hazards, technicians face a wide range of obstacles. However, through a combination of preventive maintenance, regular inspections, proper training, and the use of modern diagnostic tools, these challenges can be addressed effectively. By understanding the common difficulties faced by conveyor technicians and implementing strategies to mitigate them, businesses can ensure that their conveyor systems operate at peak efficiency, minimizing downtime and maximizing productivity.